企业推行精益六西格玛项目案例分享
什么是六西格玛呢?我们将从以下三个层面进行阐述:
第一,从企业技术管理的层面看,六西格玛是一个统计术语,是一组质量分析工具,是一系列过程控制的方法。它能准确地描述一个生产或服务过程的偏差范围和居中状况,反映产品的缺陷比率,提供质量改进的措施。
第二,从企业运营的层面看,六西格玛是一种营运战略,是一种分析问题,解决问题的方法论。当我们说一个过程或服务是六西格玛水平,就是说它是世界一流的,即每百万次出错的机率中实际只发生3.4次,而发达国家绝大多数企业产品的质量只有四西格马水平。因此,将六西格玛作为企业的战略目标可以使我们的产品和服务更具竞争力,可以把竞争对手远远抛在后面。
第三,从企业文化建设的层面看,六西格玛是一种新的思维方式,一种新的价值观。首先,六西格玛表现出对客户真正的关注,强调对客户需求动态特性的把握,认为质量是由客户定义的,让客户100%满意是企业生存和发展的前提。其次,六西格玛非常强调过程思维和基于数据做决策, 强调第一次就做好,减少返修,返工,提高滚动输出率(RTY)。
第四,六西格玛非常注重事前的预防和主动的管理。传统上实现质量目标的努力主要放在如何发现缺陷和改正缺陷上,而六西格玛则将重心放在通过过程控制和产品设计,从源头上来预防缺陷的发生。最后,六西格玛极为看重团队工作和无界限的合作。它不仅看重公司内部部门之间,上下级之间的主动沟通和合作,更强调透彻理解包括最终客户的整个工作链的需求以及使从供应商到最终客户整个供应链各方面都能获益的态度,因此它能创造一种能真正支持团队合作的管理结构和氛围。
欧倡推行精益六西格玛部分成功项目案例:
案例一:
某服装生产企业,由于精益六西格玛项目的成功推行,使企业生产效率大幅提高,从2016年的13件/天/车工,提高到目前的22件/天/车工。生产效率的提高促使企业的产品产量由2016年的每月12000dzs,每年不断提高,直到目前的每月30000dzs。
由于精益六西格玛项目的成功推行,使企业产品质量一直保持优异,客户索赔极少,进而大大提高了客户满意度。提高了企业单件流系统,WIP及库存也得到良好的控制,大货出品时间大幅减少,由2016年的50天产品出货期减到目前的25天,进而减少空运费,降低企业成本。
非直接生产员工大幅减少,车工与总人数比率提高到1:1.8。工人的平均工资从2016年开始不断上涨,直到目前的平均7300元/月;但由于效率提高,成本上涨幅度远小于工资上涨幅度,在同行业内具有很强的竞争力。
面料利用率不断提高,从2016年的82%提升到目前的86%,节省了巨额的面料成本, 为企业节源开流。
不断改进工作流程,出货/裁数比不断提高,由2016年的95%提高到目前的99.5%。存货周期不断减少,由2016年的80天左右降低到目前的45天左右。
通过技术革新,如使用伺服马达,改用天然气锅炉。。。不断降低单位能耗。通过不断提高自动化能力,提高效率,缩短新工人培训时间,降低对熟练工的依赖程度。
案例二:
某制造企业,由于很好地推行了精益六西格玛项目,企业消除了无价值的浪费,缩短了生产周期,提高了生产效率。企业以往完成全部工序从需要5人,减少至只需要2人,充分发挥个人效益。产品交付周期原来是10天(3000件),现在企业交付周期缩短50%。企业原来不能及时发现的质量问题,现在当场发现并采取防错。
采取流线化生产过程,所使需要的零件在需要的时刻、以所需要的数量不多不少地送到生产线,从根本上解决库存在物资和财务上给经营管理造成的负担。
案例三:
某防火门生产企业,由于很好地推行了精益六西格玛项目。优化了产品生产流程,精简人员由 23 /线 减为 16 /线。
完成FM 门板装潢线项目,缩短lean time 30%,节省9作业员,实现一个流作业。
现场Layout布局及物流实行流程优化,现场Line Service整合优化。
现场WIP在制品减少,操作工位,生产柔性线的设计,配料系统、操作优化。
企业装备维修基地存在着维修范围过大、周期过长、管理职能发挥不充分等缺陷,在这种背景下欧倡集团把“精益”、“价值流”和“六西格玛质量”等引入到装备维修过程中降低装备维修成本、缩短维修周期、提高维修质量。
案例四:
某家电制造行业,由于精益六西格玛项目的成功推行,该企业人均小时产量提升60%,全面地提高了企业的生产效率。;
完善PMC计划控制系统;换线时间缩短30%。
零件的移动距离明显的减小,移动的距离减小到了2900米的范围,缩减的幅度达到了原来的57%。
完善标准作业指导书,缩短了生产周期,促进了生产效率的提高。
物流速度得到了显著的提高。因为在精益六西格玛项目实施过程中对现场进行了清理,为后续的生产提供了充足的空间,所以生产过程中的产品输送速度得到了显著的提高,真正成为了精益生产的精益企业。
培养一批精益专家骨干。
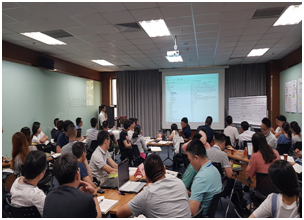
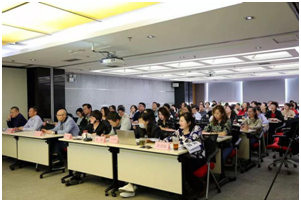
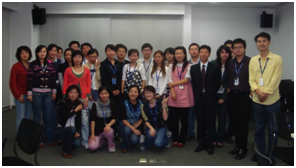
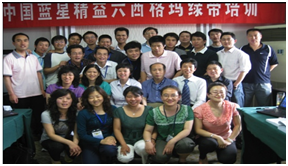
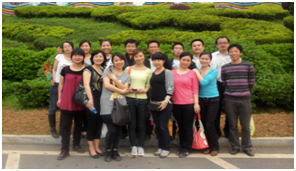
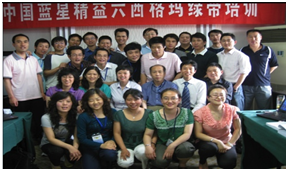
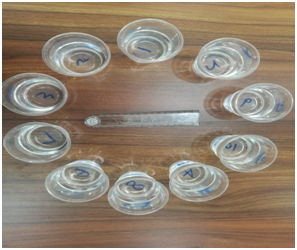
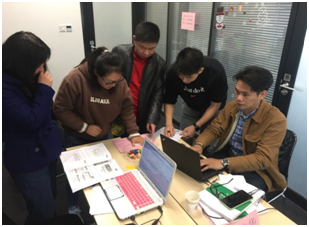
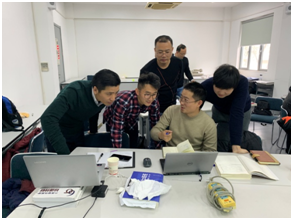